Omexom improves wind farm operations through predictive maintenance
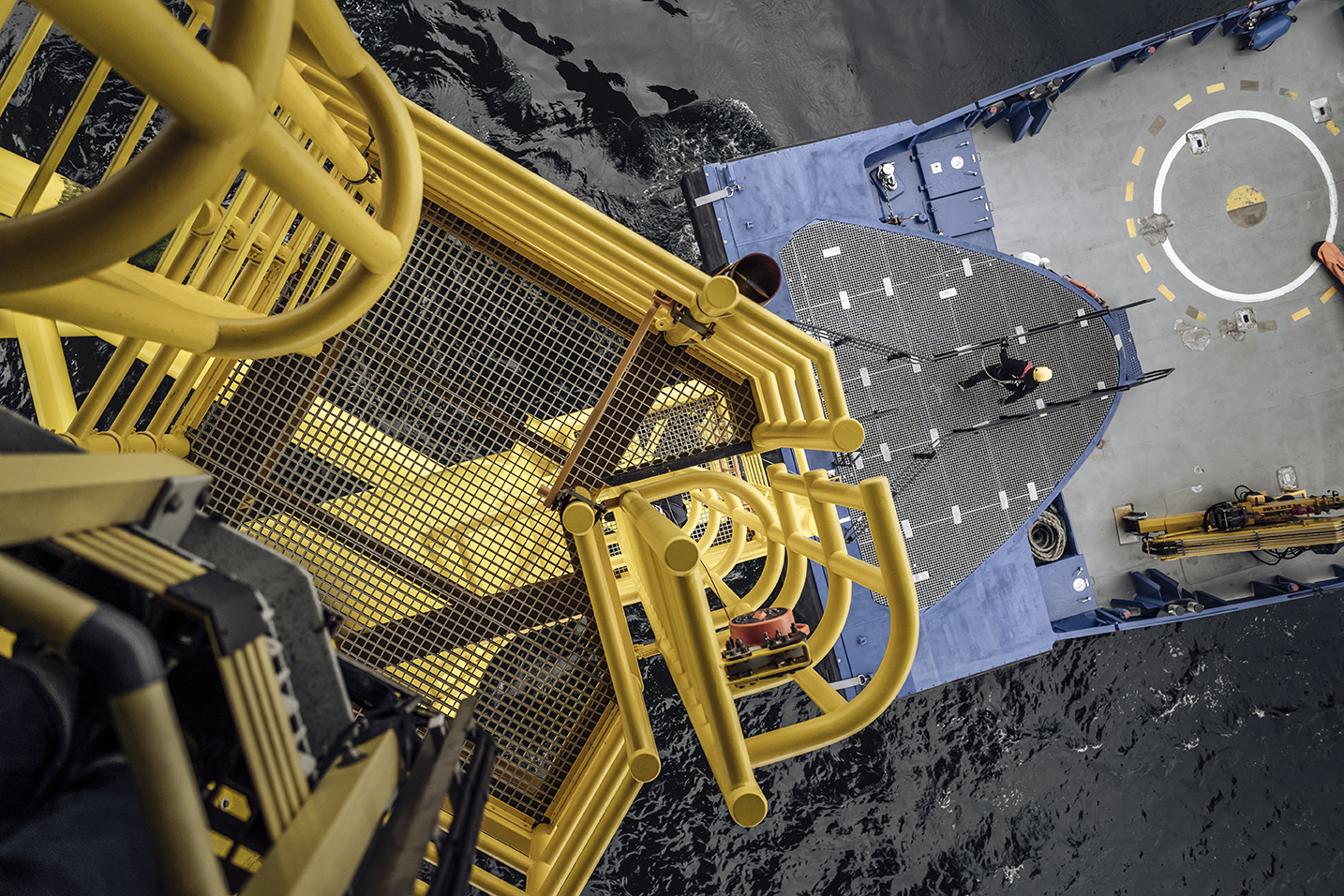
Omexom Renewable Energies Offshore, pioneer in the offshore wind industry, has joined forces with VINCI’s innovation platform Leonard, to develop a data-driven artificial intelligence solution to detect generator failures before they occur.
As the demand for green energy is increasing, investment in offshore wind farms continues to rise. Market studies predict the global offshore wind market to reach USD 56.8 billion by 2026, almost twice the amount of 2021. The International Renewable Energy Agency’s (IRENA) 1.5 °C scenario foresees an increase from the 34 GW today to 380 GW by 2030 and more than 2,000 GW by 2050.
Offshore wind: advantages and challenges
The advantages of going offshore are multiple: in the sea wind tends to be more uniform and occur at higher speeds; suitable terrain is easier to come by than on land; visual and noise impact are reduced – all these factors facilitate the construction of taller turbines and larger wind parks, thereby increasing production capacity.
On the other hand, high capital and maintenance costs and technologies that are lagging the fast development of the market make offshore wind parks a challenge.
The open sea presents harsh conditions; winds are both friend and foe: exceeding a certain speed they can lead to a shutdown of the turbines. Erosion is another common cause for turbine failure, especially as the industry pursues larger blades and expands to regions with more challenging climate.
The big problem for the main component exchanges is that the turbine stands still. Digitalisation is a great tool for us to predict possible breakdowns and will improve our processes and ensure that we produce as much green energy as possible.
Matthias Stammermann
Project Manager, Omexom Renewable Energies Offshore
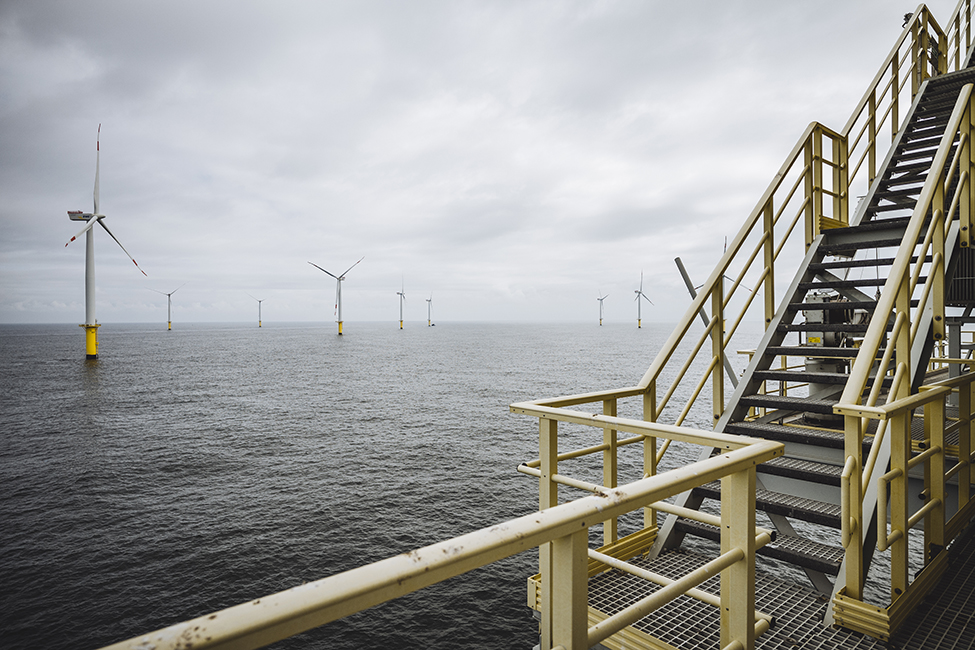
The difficulties of maintenance operations on wind turbines
Offshore wind farms are located far from the coast making them difficult or even impossible to access depending on weather conditions. For these reasons, even smaller technical issues can quickly become challenging and expensive to resolve.
This challenge is exacerbated when crucial parts of the structure are affected.
“The big problem for the main component exchanges is that we cannot predict them,” explains Matthias Stammermann, Project Manager, Omexom Renewable Energies Offshore. “When they happen, we have to react. The turbine stands still, is not producing green energy, and we have to prepare all the processes, get the material, get the vessels, and also the permissions.”
He explains that, in the example of generators, one of the most important components of the turbine, failures can cause a standstill of between 30 to 50 days. To the already significant repair costs, the financial burden related to production loss can amount to several thousands of euros a day.
Responsible for the long turnaround is the need for specific, large vessels to replace the generators, and the lack of availability and long shipping times constitute a bottleneck in the replacement works.
How predictive maintenance can help to reduce offshore wind turbine downtime
Being able to predict and anticipate generator failure would allow to plan shipments and reduce the total downtime considerably.
In the past, different technologies have been tried, but even advanced vibration monitoring solutions were unsuccessful due to noise from overlaying frequencies from other components on the same spectrum. Corrective maintenance and a scramble to reduce lost time therefore remains the status quo in most of the explorations.
Using the Riffgat wind farm in the German North Sea as a testing site, Omexom, in the framework of Leonard’s AI program, has developed another solution that may just change the future of turbine maintenance in offshore operations.
Watch the video: Preventive maintenance of generators using AI
A data-driven, digital solution with first beneficial results
In the Omexom and Leonard collaboration, already existing sensor data collected in the SCADA system of turbines working under normal conditions was used to model the behavior of each wind turbine.
This model then allows to reconstruct their behavior under normal conditions over time. The difference between the actual signal and the reconstructed normal conditions is then used to detect abnormal behavior and trigger an alarm when the difference is considerable.
The alert is then submitted to the operational manager through a user-friendly interface for validation.
Using this solution, Omexom Offshore was able to anticipate a generator exchange for the first time.
“We were very eager to join [the Leonard] program and happy that we are already getting the first beneficial results,” Stammerman said.
“Digitalisation is a great tool for us to predict possible breakdowns and if we use the smart AI concept and make use of the data we are already collecting, it will improve our processes and ensure that we produce as much green energy as possible.
Soon, Omexom Offshore plans to apply this model to other wind farms and develop it for different components, highlighting the business unit’s ambition to become an expert in predictive maintenance for offshore windfarms.